Actress Elizabeth Taylor had once famously said “big girls need big diamonds”. Smitten by the beauty and durability of diamonds, Taylor, Hollywood’s undisputed icon of glamour, had amassed an enviable collection of rare and expensive diamond jewellery in her lifetime. It’s not just Taylor. From Kate Winslet to Rihanna, and several other personalities globally have time and again publicly flaunted their fascination for the most expensive gemstone on the planet. But what is it about diamonds that make them so remarkable, captivating and inspiring for people all over the world? Perhaps it’s their time-tested beauty, strength, purity, clarity and resilience.
On that note, I recently visited the sprawling laboratory and one of the manufacturing units of De Beers Institute of Diamonds of De Beers Group, an industry leader, in Surat, and enjoyed the rarest opportunity to witness the several stages of a diamond’s journey.
Diamonds are rare crystals, which are made up of carbons, and are the hardest natural substance in the world. The final, polished stones gracefully encrust rings and necklaces or directly end up with diamond dealers. Here’s a lowdown of the rigorous process that creates value for everyone in the diamond industry.
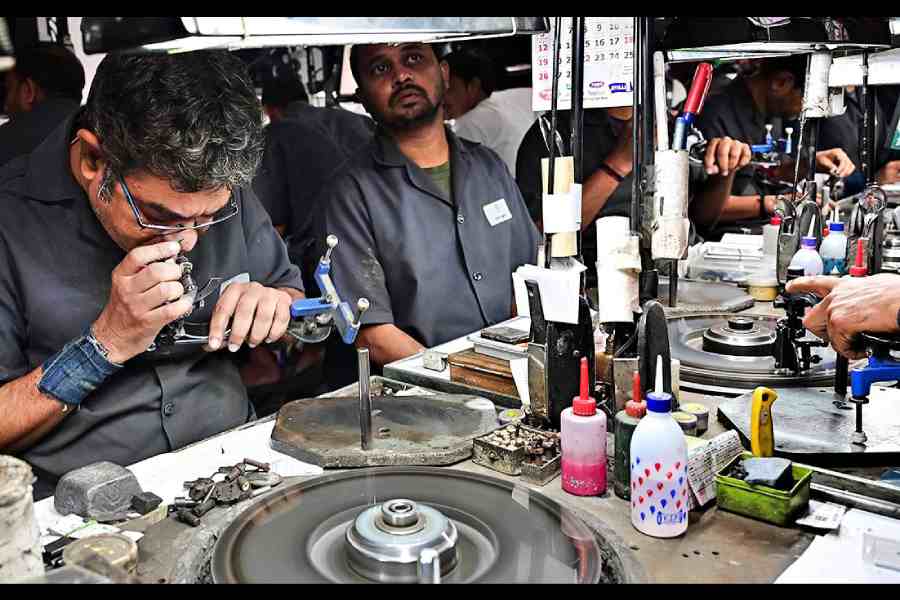
An operator inspects the stone while the polishing process is under way
On day 1, we visited one of the manufacturing units of the company where we saw how rough diamonds straight out of the mines become the final product that adorn pieces of jewellery.
The first thing we learnt is this unit makes only round-cut diamonds, the most expensive kind of diamond. Here around 250 diamonds move in every day. Gujaratis comprise 80 per cent of the workforce while the remaining are from Kerala and Tamil Nadu, among other parts of the country.
Freshly obtained rough, uncut diamonds from the mines go through the rigorous process of cutting and polishing in this unit before they move on to the lab where the certification process takes place. Depending on the best way to utilise the rough stone to the maximum advantage, it is decided how many diamonds will be carved out of it. The client’s demands are also factored in. The diamond cutter uses specialised tools to achieve the maximum result. The first step, drawing/ marking requires him to determine how a stone can be utilised to its maximum potential, using computer-aided design system and lasers.
Up next is sawing. Sawing is done in the direction of the grain of the crystal after positioning the stone over the saw. A special glue is used to hold the stone firmly in place.
Since only a diamond can cut a diamond, the blade of the saw is coated with a blend of diamond dust and oil. Smaller pieces are cut out of the big stone. In the process, the master diamond cutter cuts away the imperfections as much as possible because the higher the clarity, the higher the value. The entire process involves careful examination and re-examination at various levels using a microscope that can be 10 times the size of the stone.
For polishing, the master cutter presses the diamond against a spinning cast-iron wheel which is again coated with diamond dust and oil. At this stage too, inclusions are removed. The table facets (the flat top of the diamond’s anatomy) are designed in the desirable shape and size to achieve maximum brilliance. Then the pavilion (the V-shaped slopes that join at a point at the bottom) is polished. This process is followed by forming the crown facet and the girdle (separates the crown facets on the top and the pavilion facets at the bottom).
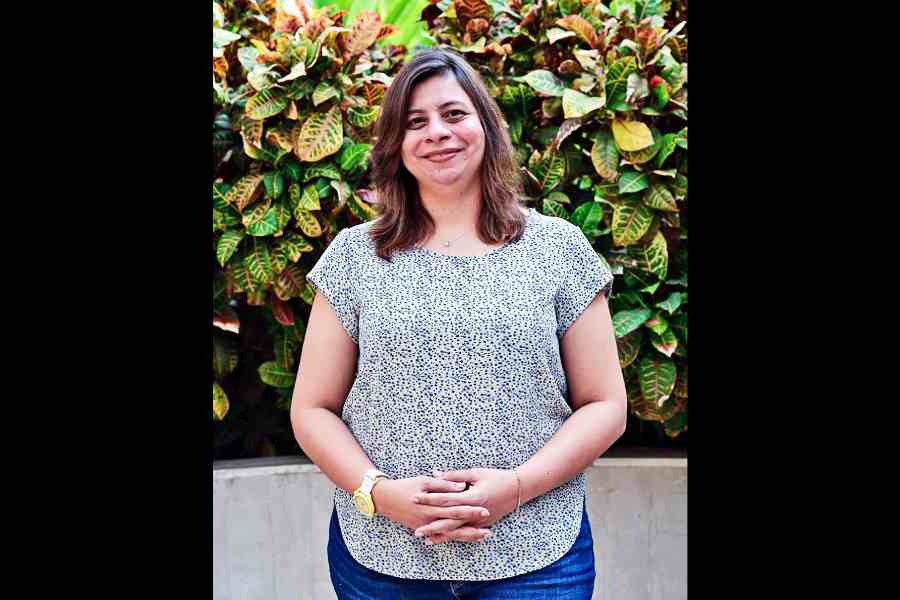
“The De Beers Institute of Diamonds, situated in Surat, only grades and inscribes natural and untreated diamonds. With cutting-edge facilities, it excels in precise diamond grading (four Cs), rigorous testing, and expert education. It stands as an unparalleled hub for the world of diamonds, seamlessly combining expertise and innovation,” said Toranj Mehta, marketing director, De Beers Forevermark
Both these processes can take up to four hours.
On the second day of our visit, we toured the sprawling state-of-the-art lab of the institute that exclusively focuses on natural diamonds. Divided into several departments that take care of the different stages of grading diamonds using 21st-century technology and techniques, the lab, adhering to the 4Cs of diamond quality (cut, colour, clarity and carat weight) weaves a diamond story for each specific stone.
The process begins with collecting the stones that are catalogued in boxes in 184 colour combinations, each marked with the institute’s unique barcoding system where each stone is assigned a unique identification number. The shipment/ stone movement is tracked at every point using a radio frequency identification system of the stone movement, and the data are verifiable at every step.
The operator will never know which stone has come from which client. The robust digitalisation ensures a safety mechanism for each stone to avoid any misplacing of stones or any kind of malpractice. The lab has the capacity to process half a million diamonds every year.
The next process involves weighing the stones. This is a crucial process which requires experts’ comprehensive analysis. The institute records up to six decimal points on its weighing scale. The operator will weigh the diamond as against the weight uploaded by the client. Now, if there is a difference between the customer-approved weight and the actual lab-approved weight, a mail is sent to the client as to whether they would like to go ahead with the weight given by the operator. If they agree, the stone moves ahead to the next process. Otherwise, it will be sent back to the client. “We want to maintain accuracy even at micro levels,” asserted a highly-placed employee who requested anonymity.
In the next step, different images of the stone are captured from different angles by rotating it through 360°. The lab has a Sarin technology in place that makes the workflow easier and more credible.
Next comes determining the colour of the stone. The grader determines the colour and the fluorescence in 10 seconds using the colour master set which ranges from D to Z. The more yellowish the tint, the less expensive a stone is. The grading starts at D, and the closer it is to D, the more valuable a stone is considered to be in the market and the price of the diamond is decided on accordingly.
Noteworthy to mention here is that each stone processed in the lab is inscribed with a unique identification number. Invisible to the naked eye, the inscription of the UIN done on the table (the upper flat portion) of the stone is an assurance of the responsible sourcing of the diamond.
Before that, the stone passes through several checkpoints. A stone can be rejected for poor table finish. If there is the slightest of stain, the operator will set it aside for further guidance from senior operators. Cleaning the table is a vital step.
Grading is a key process in the lab. Through grading, an operator determines the characteristics of a diamond. Initially, the device gives a first impression of the colour of the stone, but ultimately the human eye is required. An operator sitting on another side of the lab will not know what colour the machine has given. He will give his verdict based on his judgement. These are highly-skilled workers who have been trained enough to be able to differentiate between the closest colours which industry outsiders cannot decipher. Once he puts down his grade, he will look at what the machine has given. The task of determining a disputed colour is performed by multiple operators to achieve the highest level of accuracy. Not to mention, there are several blemishes that even machines do not recognise, but the human eye does.
For the diamond cut grading, the operator will consider several parameters, including polish, symmetry, scintillation, brightness, weight ratio, pattern, contrast, durability (includes girdles and inclusions), etc.
For the clarity part, the operator again checks for inclusions, which are birthmarks of the diamond. The degree of imperfections drives the value of the stone. The less the clarity, the less the price.